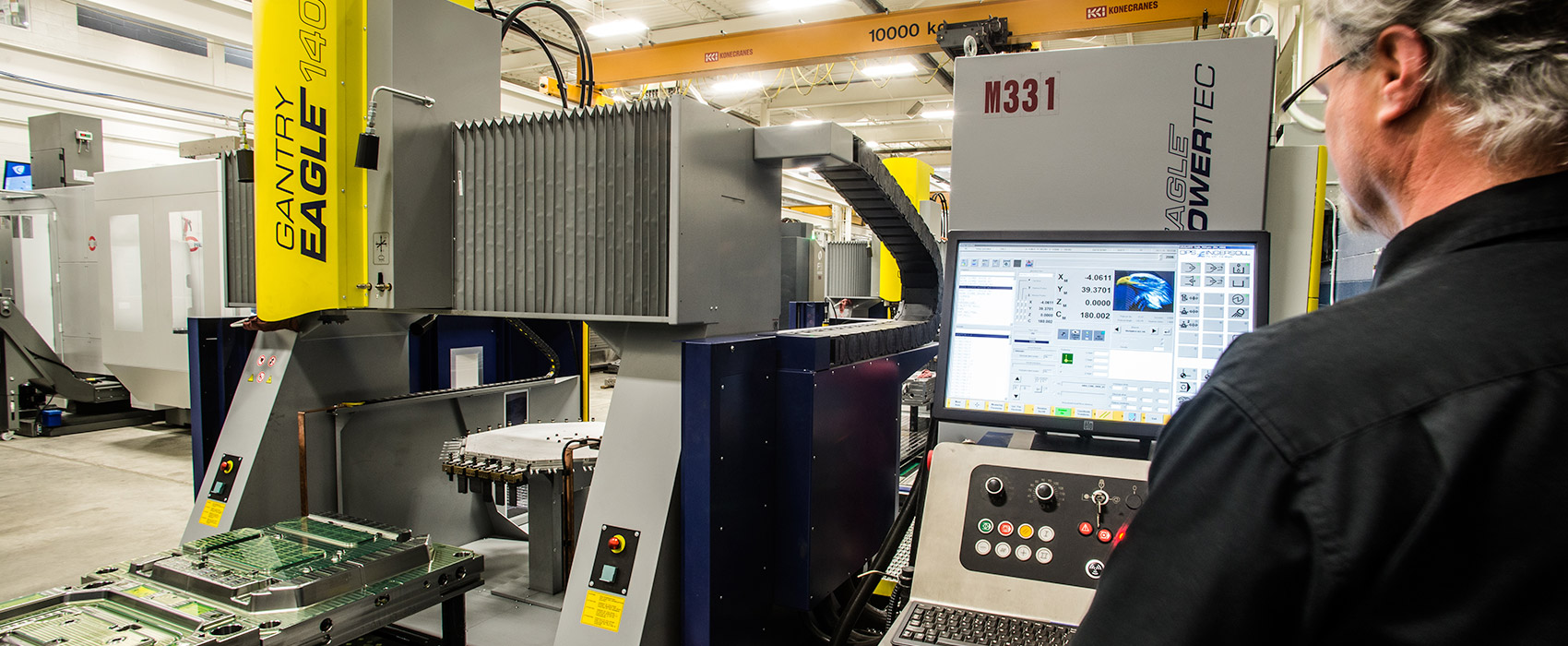
Capabilities
Cavalier Tool
has the solution
Cavalier builds molds for diverse applications, including products for the automotive, commercial, recreational, heavy truck and agricultural industries. Whether your needs are injection, structural foam, gas assist, multi-shot, thermoset, prototype or compression molds.
- Feasibility
- Design & Product Development
- Mold Flow
- Mold Manufacture & Modification
- Mold Repair Services
- Start-up services
Injection Molds
Cavalier has developed technology that greatly reduces cycle time in large, molded parts that have long flow lengths. This approach to faster cycles is accomplished with a focus on both injection and cooling profiles. Unique drop positions and angles shorten and balance melt flow within the part geometry. Specialized cooling line techniques that include unique materials, balanced channels and unlimited cooling line patterns within printed mold components, greatly reduce the cooling cycle. We have achieved production rates that are 2 or 3 times faster than that of traditional hot runner and cooling design concepts.
Aluminum Molds
Aluminum molds have increasingly been used in mass production of automotive parts as well as large, plastic home appliance components such as washing machine tubs and commercial products including plastic pallets. Some unique benefits include high thermal conductivity and superior machinability. Aluminum mold alloys have about four times higher thermal conductivity than mold steels dramatically reducing cooling time in injection molding and minimizing local hot spots that result in part distortion and degraded exterior surfaces. It also helps deliver simpler coolant channel design. Aluminum molds also can be machined faster and polished rapidly.
Gas Counter Pressure Molds
Counter pressure can be best described as an extension of modification of the stand injection molding process, the difference is how the melt front of the incoming resin is controlled. Counter pressure provides a controlled resistance to the flow front, forcing some of the melt to enter the thinner or harder to fill areas during the initial injection. It can also aid in keeping unwanted volatiles from breaking through the flow front. The gas used to develop the counter pressure pushes on the melt front during injection. Surface imperfections such as splay, glass fibres, colour streaks and surface blisters can often be eliminated.
Compression Molds
Compression molding is typically utilized for heavy walled applications requiring high strength and durability that may incorporate other materials. These materials can be in the form of a substrate like a glass mat roving or molded in fibres of various materials. The advantages can be lower mold costs for shorter runs and less complex mold construction. Many markets utilize compression molded parts for structural applications in automotive, heavy truck, recreational and agricultural vehicles, infrastructure and many others.
Injection Compression Molds
Injection compression molding is a method of creating uniform properties, typically with long fibre-reinforced plastics. This is done by changing the volume of the cavity during the molding process, essentially closing the mold completely only after the plastic material is already in the mold. With the mold slightly open the shot is injected into the open cavity which allows material to travel over most of the part rather than flowing through wall stock. The mold is then closed “compressing” the shot to form the final part shape. Shrinkage and deformation effects are reduced, uniform pack and melt compression allows for greater rib/wall ratios with fewer sink marks and greater molding precision.
Multishot
Multi-shot (or two-shot) molding is the process of physically bonding two different materials into one component within one manufacturing process. A proven technology that is used across many industries, multi-shot molding allows multiple materials to be injected into separate locations on the same mold. Different surfaces, even incompatible materials, can be securely bonded into a single component that is stronger and more durable than its two-piece counterpart.
Structural Foam
Structural foam molding is a low pressure injection molding process where gas is introduced into melted polymer for the purpose of reducing density and weight of the finished product while increasing the strength. The structural foam molding process utilizes a resin that has been injected with gas then into the mold, where the gas expands and fills the mold with foam. As the foam flows through the mold, the surface cells collapse. Solid skins are formed against the walls of the mold, while the core of the part remains structurally foamed. Because the outer skin is solid and the center of the wall is foam, the part weight is reduced up to 20%. Structural foam yields parts that are larger and sturdier than injection molding. The process pressures are much lower than in injection molding, thereby requiring less steel and reducing mold cost. Aluminum is often used to increase cooling to reduce cycle times. Parts tend to be, nearly stress-free and have minimal warpage. Parts also cycle faster than convention examples of similar thicknesses due to reduced resin content.
Stack Mold
Stack Molds are a series of mold faces that are “stacked” together to create multiple levels for molding, either 2 or 4 level. The advantage of stacking parts is to be able to mold 2 to 4 times more projected area in the same tonnage as a single face mold. The projected area of one face offsets the tonnage of the adjacent face. Special press considerations are required to run stack molds, such as platen daylight, mold open stroke and shot size. Specialized hot runners, and mold centering devices are also a requirement for stack molds.